واحد های تولید در شرکت آبین گستر شرق
فرآیند تولید فیلتراسیون در مجموعه آبین گستر شرق گرمسار در فضایی به مساحت 5000 مترمربع در قالب واحد های زیر انجام میشود
1 ) واحد انبار
تعریف انبار و انبارداری
سرپرست انبار:
فردی آشنا به دانش انبارداری و حسابداری است که یک یا چند انبار بزرگ یا کوچک را سرپرستی و اداره می کند.
انباردار:
مسئول یا متصدی یک انبار می باشد که مأمور تخلیه و تحویل کالای جدیدالورود ، چینش و انبارش آن کالا و بارگیری و تحویل کالا به متقاضی حسب دستور مافوق و با اخذ حواله مستند و مدلل
انباردار در شرکت آبین گستر شرق گرمسار به برنامه حسابداری صنعتی آشنا میباشد و ارتباط مستقیم با واحد مالی دارد تا موارد لازم جهت بروزماندن انبار و حسابداری صنعتی بدرستی انجام شود .
وظیفه انبار:
هر انبار سه وظیفه مهم دارد:
۱- تهیه کالا یا مواد مورد نیاز سازمان یا شرکت ( تحویل گرفتن و وارد کردن آنها )
۲- نگهداری آنها به شیوه علمی و دستورالعملهای مالی و حتی داخلی
۳- توزیع کالا یا مواد انبارش شده در انبار بر اساس مجوزها
وظایف انباردار:
۱- بررسی نیاز و سفارشات جدید و درخواست ترمیم موجودی کالای رسیده به نقطه سفارش
۲- ارسال درخواست خرید تنظیم یافته به واحد سفارش ها و تدارکات
۳- چینش صحیح و علمی کالا در انبار
۴- مراقبت و صیانت از کالاهای انبارش شده
۵- تهیه و تحویل کالا و ثبت در دفاتر و کارتهای مربوطه
۶- توزیع به هنگام بر اساس مجوز ( حواله )
انبارش:
به مدیریت انبارداری اعم از انباشتن ، چیدمان و حسابرسی تا ترخیص کالا و حسابداری خرید و فروش و تنظیم اسناد مربوطه و نهایتاً به روز رسانی مدیریت انبارداری به روشهای نوین علمی ، انبارش گفته می شود و دارای پنج گام می باشد : « چینش – سنجش – ارزش – گزارش – پردازش »
چینش:
به چیدمان کالا در انبار به روش علمی چینش اطلاق می گردد.
در ابتداء باید کالا را به لحاظ ماهیت ، فرم ، وزن و حجم و دیگر شاخص ها شناسایی کرد و سپس به تناسب اندازه و جرم و تعاریف طبقه بندی کدینگ درون انباری بررسی نمود.
کالاهای وزین ، سنگین در طبقات زیرین و پایینی قفسه ها قرار می گیرد ؛ کالاهای زود مصرف باید در دسترس بوده و کالاهای دیر مصرف و با کم مصرف در قفسه های ردیف های بعدی و انتهایی گذاشته می شود. و کارتن ها و بسته های سبک و کم حجم در طبقات بالاتر و به تناسب کم مصرف بودن در طبقات فوقانی تر قرار می گیرد ، امّا با چیدمانی مستحکم که با تکانهای جزئی و زمین لرزه های خفیف از بالا به پایین سقوط نکند.
جدا سازی کالاهایی که در کنار هم ، موجب واکنش شیمیایی می گردد و یا در هم جواری هم باعث تخریب هردو و یا یکی از آنها می شود و نیز متأثر در طعم و مزه ، بو و نظایر آن می شود و همچنین باید کالا چنان در کنارهم چیدمان گردد که ضمن حفظ ماهیت تقابل آنها، انباردار به سهولت به کالا مشابه یا هم گروه و هم خانواده دست یابد.
سنجش:
بررسی میزان موجودی و سطح سفارش ، سنجیدن کالا به لحاظ عملکرد انبار در خصوص لایفو و فایفو و شناسایی کالاهای پر مصرف و کم مصرف و تمیز دادن کالاهای دیر مصرف از بدون مصرف ( بلا استفاده ) و تعیین نفاط حداقل و حداکثر موجودی و نقطه سفارش و جلو گیری از افت و کاهش کالا به میزان تعریف شده در نقطه ی حداقل موجودی و ممانعت از افزایش موجودی و تجاوز از میزان حداکثر موجودی و دیگر موارد.
گزارش:
تنظیم کلیه اسناد اعم از قبوض رسید انبار و حوالجات خروجی انبار و صدور درخواست خرید ، ارائه لیست یا سیاهه کالاهای کم و پر مصرف و اعلام وجود کالاهای دیر مصرف و بلا مصرف به مقام یا مقامات بالاتر
تنظیم جدول کار و تفکیک مسؤولیت هر یک از پرسنل انبار در امور پنجگانه ( نظافتی – خدماتی – اداری -نظارتی و حفاظتی ) و تنظیم جدول حلقه حفاظتی و ملزم نمودن مجری هر بند آن در بدو ورود و هنگام خروج از انبار
پردازش:
به روزرسانی دانش انبارداری ، آموزش عمومی انبارداری و امورمالی کلیه پرسنل انبار و آموزش تخصصی به هریک از کارکنان انبار در راستای شرح وظایف محوله به آنها ، جمع آوری و پباده سازی سیستم هایی چون نصب برنامه درخواست الکترونیکی ، صدور حواله خروجی با بارکد خوان ، بیمه نمودن انبار در برابر حوادث و سرقت تهیه و نصب سیستم اطفای حریق و هشدار دهنده و تهیه ابزار و ادوات جدید و کاهش حجم کار و بار ترافیکی آن و دیگر مواردی چون JIT به ویژه در انبارهای دولتی با کاربری غیر بازرگانی به منظور کوچک سازی انبار و مجازی کردن آن به منظور پرهیز از احتکار کالا و انباشتگی غیر استاندارد که پیامدهای چون تخریب و یا نزدیک شدن کالا به تاریخ انقضاء و یا دموده شدن و منسوخ شدن آنها و نیز یا وجود فراونی اجناس مشابه و با کیفیت و قیمت مناسب تر در بازار و نظیر آن
مواد و قطعات اولیه قبل از استفاده در واحد تولید توسط کارشناس کنترل کیفیت بازرسی شده سپس به واحد انبار تحویل داده میشود .
در واحد انبار متناسب با سفارش ساخت های موجود قطعات و مواد موردنیاز به واحد تولید تحویل داده میشود .
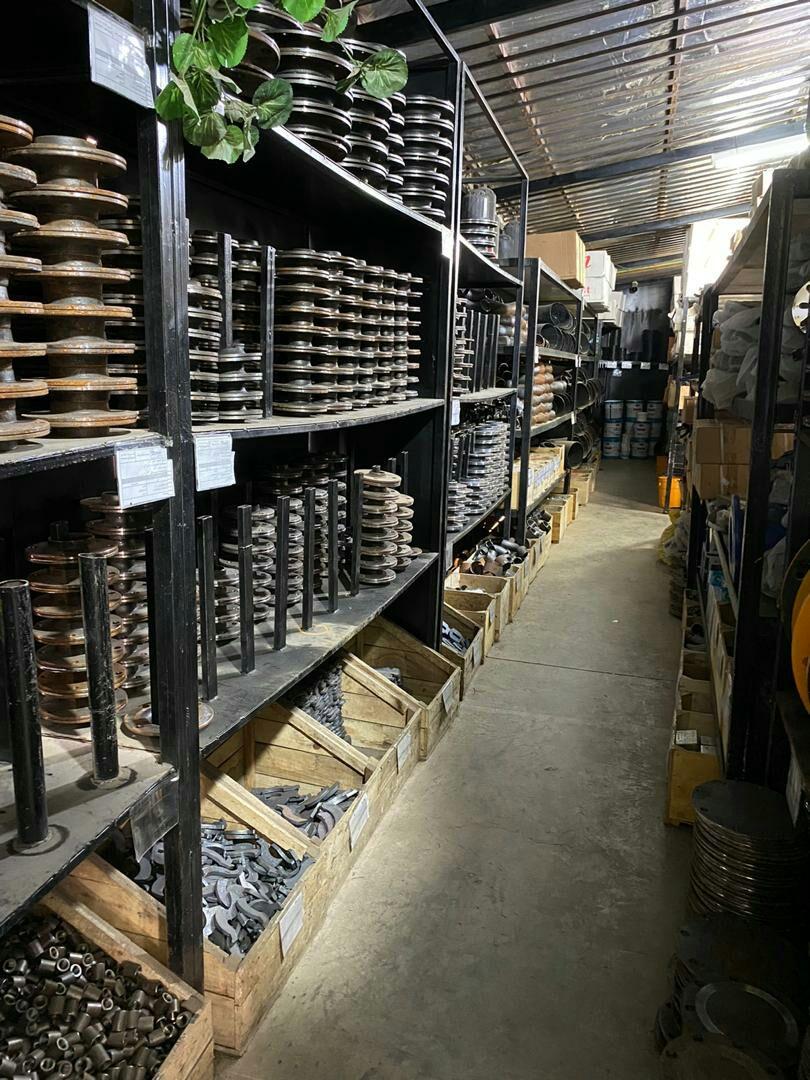
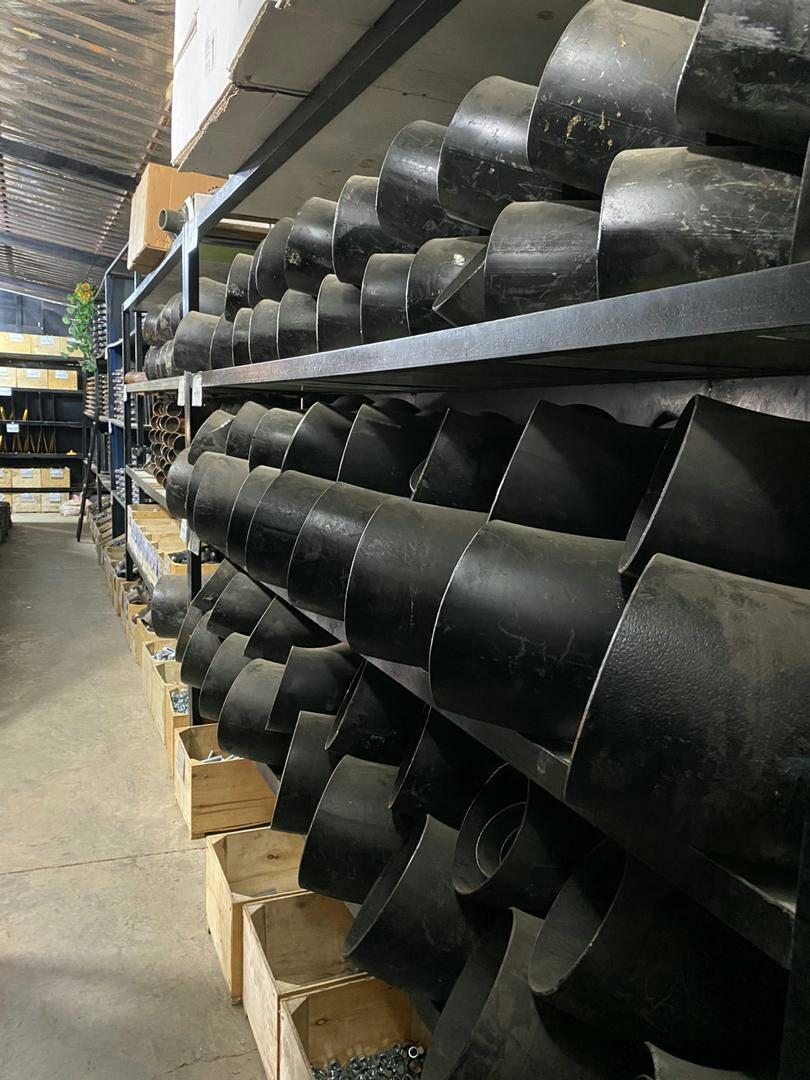
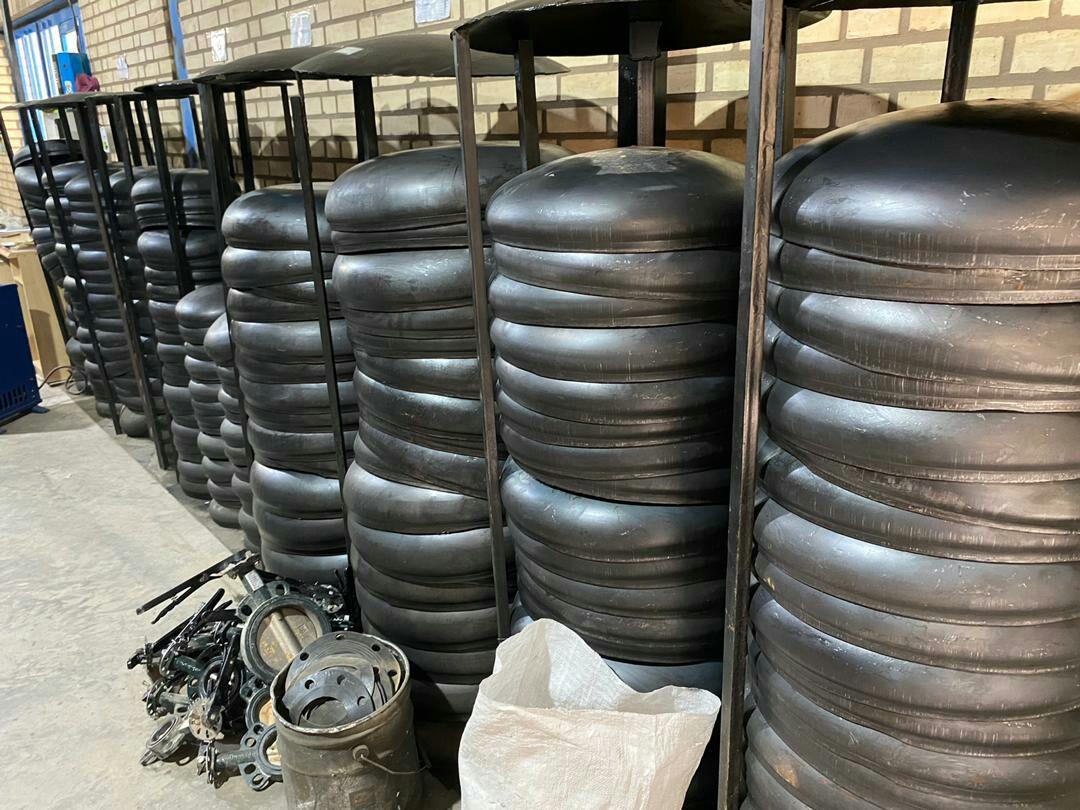
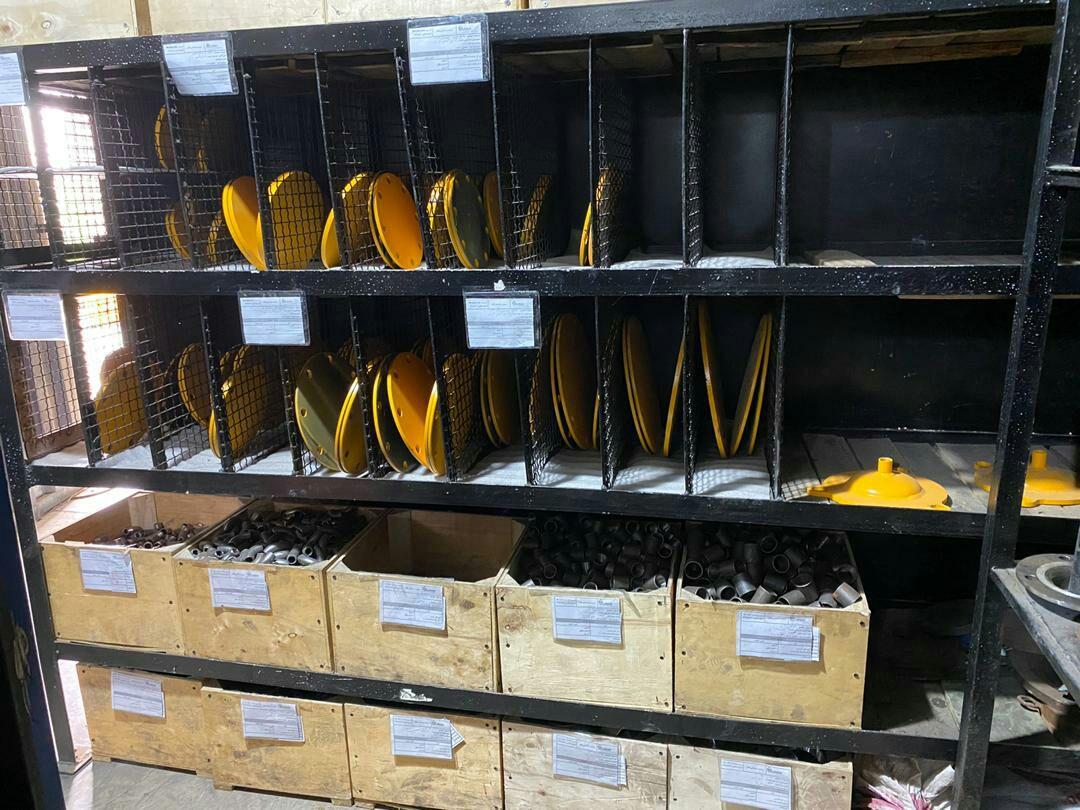
2 ) واحد برشکاری
برشکاری هوابرش و یا هواگاز چیست؟
هوا برش و یا همان برش هوا گاز و جوش اکسیژن – سوخت گاز از روش هایی مرسوم و نسبتا ارزان قیمتی میباشند که در آن ها سوخت ینی همان گاز به همراه اکسیژن برای عملیات جوش دادن و یا برش دادن انواع فلزات مورد استفاده قرار میگیرد. در واقع از این روش هم برای برشکاری و هم برای جوشکاری استفاده میشود.
اولین بار آقایان Edmond Fouché و Charles Picard در سال ۱۹۰۳ از این روش برای جوش دادن استفاده کردند. این مهندسین فرانسوی از اکسیژن خالص به جای هوا برای ذوب قسمتی از فولاد استفاده نمودند. شعلهی حاصل از این عمل دمایی در حدود ۲۰۰۰ تا ۴۰۰۰ درجهی سانتی گراد ایجاد مینماید.
برای جوش دادن قطعات از روش اکسیژن – سوخت گاز استفاده می شود. البته این روش قدیمی است و امروزه کمتر به کار میرود. در حال حاضر از این روش برای جوش دادن لوله ها، استفاده جهت تعمیرات و ساخت کارهای هنری استفاده میشود.
برای برش هوا گاز از یک مشعل برش جهت پاشش یک گاز ( استیلن) به محل برشو ایجاد حرارت در فلز تا دمای برافروختگی استفاده میشود. سپس یک جریان اکسیژن به روی فلز دمیده میشود و فلز در این اکسیژن سوخته و اکسید شده و سپس فلز به صورت گل اکسیدشده به بیرون از محل برش جاری میگردد.
در برشکاری هوا برش از گاز اکسیژن و استیلن استفاده میگردد. اکسیژن دمیده شده با فلز داغ واکنش میدهد و تشکیل اکسید داده و تولید گرما و حرارت مینماید. گرمای تولید شده باعث پیوسته شدن عمل برش در قطعهکار میشود. در نتیجه شعله مشعل فقط آغاز برش را ایجاد مینماید و دمای مورد نیاز در طی فرآیند تامین میگردد. نقطه ذوب اکسید آهن تقریبا برابر نصف مقدار نقطه ذوب آهن است. زمانی که آهن شروع به اشتعال میکند، بلافاصله به اکسید آهن مایع تبدیل میشود و به تدریج به خارج از ناحیه برش جریان پیدا می کند. اما مقداری از اکسید آهن بر روی قطعه کار باقی می ماند و تبدیل به گل (خاکستر) سخت روی کار می شود که با ضربه ی آرام یا سوهان کاری از قطعه جدا می شود.
از این روش برشکاری مانند روش برش پلاسما در دستگاه های برش cnc نیز میتوان استفاده نمود. از مزایا این روش قابلیت برش با ضخامت های نسبتا بالاست. یکی دیگر از مزایا این روش قابلیت برش بر روی تمام فلزات است در حالی که در روش برشکاری پلاسما فقط میتوان فلزات رسانا بویژه فولاد را برش داد. همچنین میتوان لبه های برش دقیق تری را داشت.
تجهیزات کلی دستگاه هوابرش
کپسول های گاز مربوطه – رگولاتور – شیلنگ های گاز – شیر یک طرفه – مشعل – نازل
در شرکت آبین گستر برشکاری توسط دستگاه برش CNC پلاسما توسط اپراتور متخصص و آموزش دیده صورت میگیرد .
در ادامه ورق و لوله های بریده شده در اختیار واحد تولید قرار میگیرد .
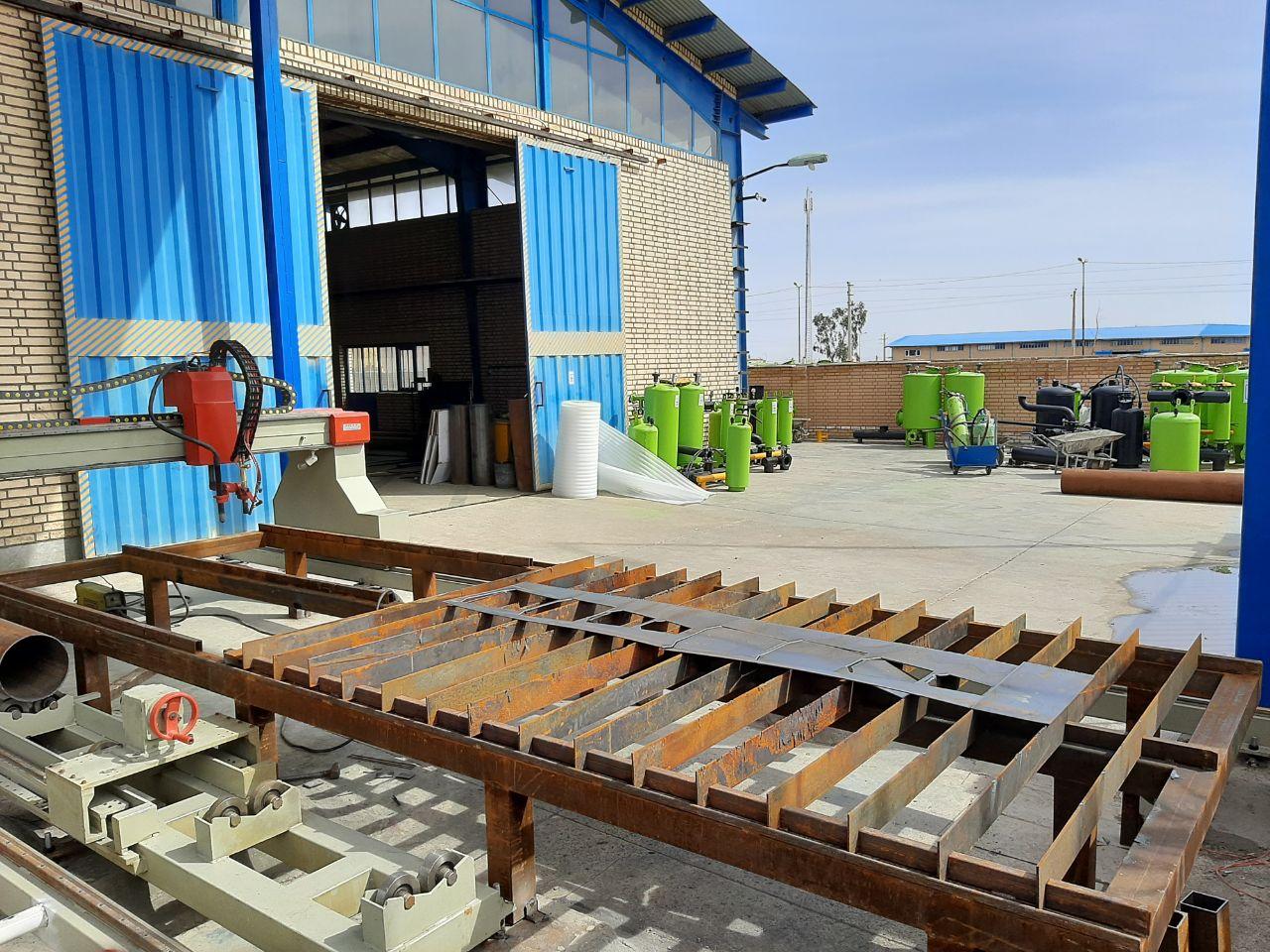
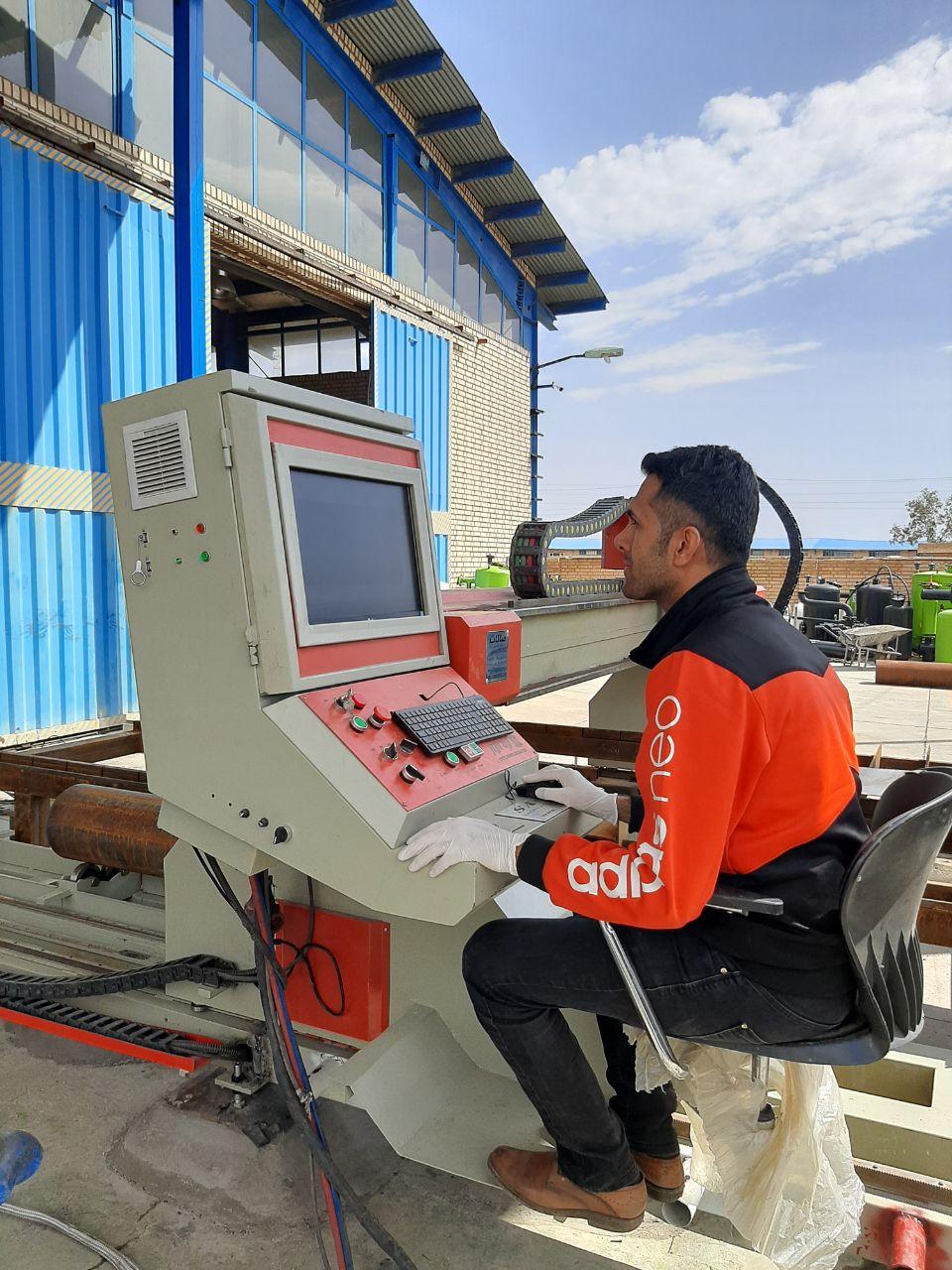
3 ) واحد نورد
نورد
یکی از روش هاي مهم شکل دهی، نورد است که در این روش از حجم شمش یا فلزي که شکل داده میشود چیزي کم نمی شود. به عبارت دیگر براده برداري از فلز انجام نمیشود. تغییر شکل در این روش بدین صورت انجام می گیرد که شمش مورد نظر پس از گذشتن از بین غلطک هایی که در جهت عکس یکدیگر حرکت می کنند به شکل مطلوب تبدیل خواهد شد.
اگر فلز عبور داده شده از بین دو غلطک گرم شده باشدبه شکلی که داراي دماي حدود ۱۱۰۰ درجه سانتیگراد باشد، نورد را گرم می نامند. گرم کردن باعث نرم شدن فلز و در نتیجه کاهش نیروي لازم براي نورد می شود. اگر تغییر ضخامت یا سطح مقطع فلز پس از نورد کم باشد، دیگر نیازي به گرم کردن نیست و البته نورد گرم نمی تواند براي چنین ورقی ابعاد دقیق و سطحی صاف و بدون موج بدهد نورد بدون گرم کردن یا نورد سرد در ذوب آن اصفهان انجام نمی شود و تمام کارگاه هاي نورد ذوب آهن عملیات را در حالت گرم انجام میدهند با توجه به اینکه کارگاه هاي نورد ذوب آهن مقاطع ساختمانی مانند تیرآهن، نبشی، میلگرد و سیم تولید می کند،نیاز است غلطک هاي نورد داراي شیارهایی باشند که به مرور و با گذر شمش از هر کدام از آن ها، سطح مقطع به محصول نهایی نزدیک و نزدیک تر شود به سطح مقطع حاصل از قرار گرفتن قرینه دو شیار از دو غلطک که روي هم یا کنار هم قرار گرفته اند، کالیبر میگویند.وقتی شمش از کالیبر عبور می نماید شکل و اندازه کالیبر را به خود میگیرد. پس از عبور فلز از چندین کالیبر، پروفیل مورد نظر بدست می آید به عبارت دیگر شمش به محصول نورد تبدیل خواهد شد.
تاریخچه نورد
شروع فرایند نورد به قرن هفدهم میلادی میرسد . در قرن هفدهم به صورت ساده ۲ غلتک چدنی را در یک چهار چوب چوبی قرار داده و با عبور قلع و سرب از بینشان و کاهش سطح مقطع آنها عملیات نورد را انجام می دادند.
به مرور از غلتکهای بزرگتری استفاده کردند که که به وسیله اسب و یا پره های آبی به حرکت در می آمد.استفاده از شیار برای شکل دادن به محصول نورد شده نیز مربوط به این دوران است .
سپس برای کاهش نیروی لازم جهت چرخاندن غلتک ها، به جای غلتک های بزرگ از غلتک های کوچکتری که با غلتک بزرگتری چرخانده می شود استفاده شد و به این ترتیب قفسه های چهار غلتکه به وجود آمدند .
بعد از اختراع ماشین بخار محدودیت نیرو از بین رفته و قفسه های نورد بزرگتر شده واز ماشین های بخار قوی جهت نورد شمش ها استفاده شد .با پیشرفته تر شدن وصنعتی شدن صنعت نورد، این صنعت به عنوان جایگزین برای دیگر روش های شکل دادن فلز ها در آهنگری و پخته گری گردید.
در کنارفرایند نورد دیگر بخش های کارخانجات نورد همچون کوره های ذوب ماشین های ریخته گری برای آماده سازی شمش های اولیه ، کوره های پیش گرم برای گرم کردن شمش ها ، خطوط جابجایی ،حمام های اسیدشویی ، کوره های عملیات حرارتی ، حمام های آبکاری ماشین های بسته بندی و … نیز روند تکاملی خود را پیمودند.
انواع نورد
نورد محصولات فلزی به دو روش صورت میگیرد
نورد گرم
نورد سرد
نورد گرم
در نورد گرم فلز از بین دو غلتک که فاصله ی بین آنها اندکی کمتر از ضخامت فلز ورودی و خلاف جهت یکدیگر چرخانده می شوند عبور داده می شود.به دلیل بیشتر بودن سرعت چرخش غلتک ها از ریلی که فلز روی آن قرار دارد، اصطکاک بین غلتک و فلز موجب به جلو راندن فلز شده و طول آن را افزایش و ضخامت آن را کاهش می دهد.
مقدار کم شدن ضخامت در طی نورد بستگی به میزان اصطکاک بین غلتک و سطح فلز دارد به نحوی که برای تغییر شکل زیاد غلتک ها به جای حرکت ماده روی آن می لغزند.
نورد سرد
ورق هایی که از طریق نورد گرم با حداقل ضخامت تولید می شوند روی آنها پس از اسید شویی، عمل کاهش ضخامت و یا تغییر شکل از طریق فرایند نورد سرد انجام می پذیرد. پس می توان گفت، کاربرد نورد سرد کاهش ضخامت با دقت ابعادی مورد نظر ورق های فولادی می باشد.
نقطه تسلیم چیست؟
نقطه تسلیم باعث بوجود آمدن شرایط تغییر شکل ناهمگن در فرآیند شکل دادن و به ویژه کشش عمیق می شود که حذف آن از موارد مهمی می باشد و انجام چندین کار مکانیکی توسط نورد که به آن نورد بازپخت می گویند باعث حذف نقطه ی تسلیم می گردد.
تعریف قفسه:
براي اینکه غلطک هاي نورد بتوانند نیروي لازم را به شمش اعمال کنند نیاز است که روي تجهیزات فلزي نصب شوند به شکلی که، هم بتوان نیروي چرخشی به آنها اعمال کرد و هم فاصله غلطک ها و کالیبرهاي را تنظیم نمود. این تجهیزات فلزي را قفسه مینامند.

مزایا و معایب نورد گرم
مزایا و معایب نورد گرم عبارت است از
به نیروی کمتری در طی فرآیند نسبت به نورد سرد احتیاج است
تجهیزات و دستگاههای کمتری برای نورد گرم مورد نیاز است
کرنش سختی کمتری در طی فرایند روی قطعه انجام می شود .
قطعه ی فلزی تولید شده دارای استحکام کمتری نسبت به محصولات تولید نورد سرد است
نورد گرم برای شمش های بزرگ مناسب است
و…….
به منظور آماده شدن بدنه فیلترهای شن ، تانک کود و هیدروسیکلون ورقهای بریده شده در مرحله قبل توسط دستگاه نورد آماده شده و به مرحله بعد در تولید تحویل داده میشوند .
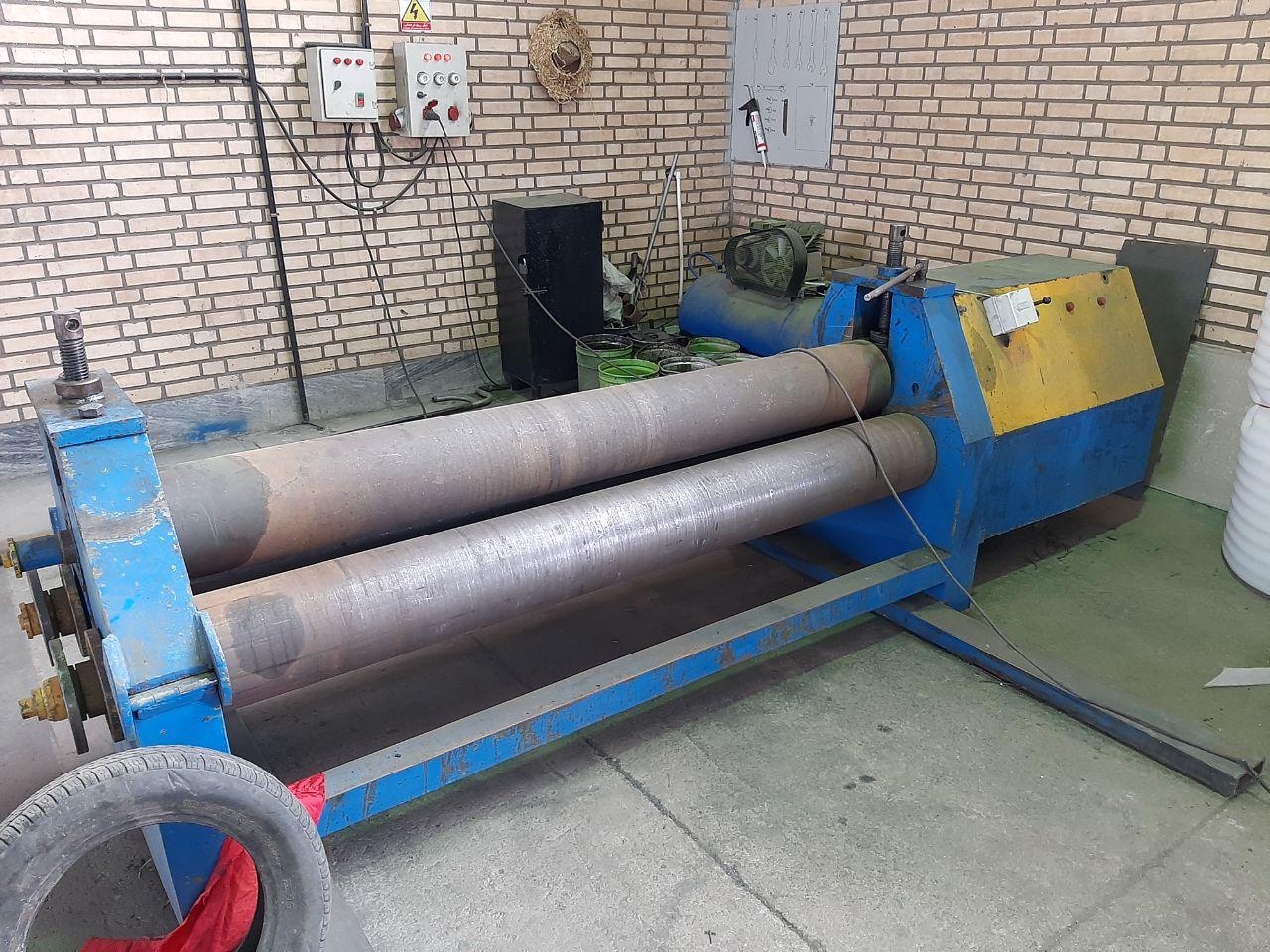
4 ) واحد لبه و پرس
یکی از دستگاههایی که میتوانند نقش متفاوتی در تولید قطعات داشته باشد، دستگاه پرس است که هم در متراکم کردن مواد مختلف و هم در شکلدهی آنها به کار گرفته میشود. این دستگاهها به اندازه دستگاه فرز cnc یا دستگاه تراش سی ان سی پیشرفته نیستند، اما در برخی موارد خاص عملکرد آنها نسبت به دستگاههای سی ان سی بسیار مناسبتر است. از طرف دیگر کار با دستگاههای پرس نسبت به این دستگاهها سادهتر بوده و امکان استفاده از آن در حوزههای مختلف وجود دارد.
دستگاه پرس چیست و چگونه عمل میکند؟
کلمه پرس از واژه انگلیسی Press به معنی فشار دادن و متراکم کردن برگرفته شده است. بنابراین دستگاه پرس یک دستگاه مخصوص برای وارد آوردن فشار تحت کنترل بر روی یک جسم خاص است که امکان متراکم کردن و شکل دهی آن را فراهم میکند. البته این به این معنی نیست که دستگاههای پرس در همه شرایط برای متراکم کردن هستند، بلکه در برخی موارد کار آنها صرفاً شکل دادن و نگه داشتن نمونه برای تغییر حالت آن است. منشاء فشار ورودی در این دستگاهها متفاوت است و نسل اولیه آنها با استفاده از نیروی مکانیکی و با دست اعمال میشد.
نحوه عملکرد دستگاه پرس به این صورت است که دارای یک سطح به عنوان میز به عنوان نگهدارنده قطعه کار است. در طرف مقابل هم یک ابزار قرار دارد که با استفاده از یک اهرم، فشار لازم را به سطح قطعه کار وارد میکند. این فشار در دستگاههای قدیمی با استفاده از نیروی دست و نیروی انسانی اعمال میشد، اما امروزه از دستگاههای هیدرولیک و دستگاههای پنوماتیک برای ایجاد این فشار استفاده میشود. نحوه عملکرد این دستگاهها به شکلی است که فرد میتواند میزان فشار وارده بر روی یک سطح را اندازه گیری میکند و به نوعی فشار کنترل شده به آن اعمال کند.
انواع دستگاههای پرس موجود در بازار
اگرچه معیارهای مختلفی برای دسته بندی دستگاههای پرس وجود دارد، اما اصلیترین و مهمترین ویژگی در دسته بندی آنها، منشأ فشار است. فشار ممکن است توسط عوامل مختلفی مانند پمپهای هیدرولیکی یا پمپهای پنوماتیکی به وجود بیاید. بنابراین دستگاههای پرس در دستههای زیر قرار میگیرند:
دستگاه پرس هیدرولیک
دستگاههای پرس هیدرولیک از ابزارهای برقی هستند که فشار آنها با استفاده از فشار هیدرولیک تأمین میشود. فشار سیال در یک محفظه خاص، با استفاده از پمپها و شیرآلات مختلف میتوانند افزایش یا کاهش یابد. بعضی اوقات ممکن است از دستگاهها و سیستمهایی برای افزایش ظرفیت پمپها در پروسههای قدرتمند استفاده شود. این پرسشها میتوانند در ابعاد بزرگ و برای کار با سرعت ثابت استفاده شوند.
نحوه عملکرد دستگاه پرس هیدرولیک تقریباً همانند ترمزها و فرمانهای هیدرولیک است که انتقال نیرو با استفاده از مایع هیدرولیک انجام میشود و به همین دلیل سرعت آنها نسبت به دستگاههای معمولی کمتر بوده و نیاز به کار طولانیتر دارند. به هنگام استفاده از این دستگاهها شما باید مسئله گرم شدن قسمت مرتبط با نیروی هیدرولیک را در نظر داشته باشید. این دستگاهها را میتوان قدرتمندترین دستگاه پرس معرفی کرد که قادر به اعمال نیروی ۷۵ هزار تن نیرو است.
در تصویر زیر از یک دستگاه پرس هیدرولیک یک نمای شماتیک میبینید. البته این نما مربوط به دستگاه پرس عمودی است و ممکن است نمونههای افقی آنها را هم در بازار ببینید. استفاده از دستگاههای پرس هیدرولیک بسیار ساده است و به تفاوت در فشار مایع هیدرولیک متکی است. مایعات درون سیلندر زیر پیستون پمپ میشوند و این باعث میشود که فشار سیار بر روی پیستون افزایش یابد. به طور همزمان، مایع از کانال فوقانی پمپاژ میشود و فشار سیال با شدت بسیار زیادی به سطح دستگاه وارد میشود.
در مرحله بعد، مایع زیر پیستون پمپاژ شده و باعث میشود که فشار زیر پیستون کاهش یابد. به طور همزمان مایعات از بالا به داخل سیلندر پمپ میشوند و این باعث افزایش فشار سیال در بالای پیستون میشود. نتیجه این فعل و انفعالات حرکت دادن دستگاه های پرس به سمت پایین و فراهم آوردن فشار بیش از حد و قابل کنترل است.
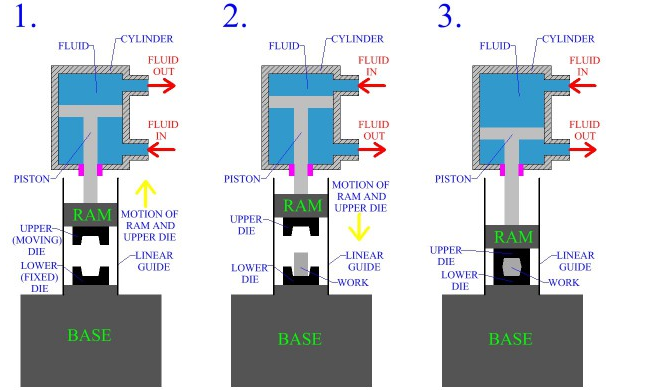
دستگاه پرس مکانیکی
دستگاههای پرس مکانیکی متعلق به گروهی از ماشینآلات هستند که نیروی پرس کننده با استفاده از نیروی چرخشی یک موتور یا با سایر شیوهها تأمین میشود. در مرحله اول، نیروی چرخشی یک موتور یا یک الکتروموتور توسط یک مبدل به یک محور اعمال میشود که عمل فشار را انجام میدهند. بنابراین انرژی در پرس مکانیکی از موتور حاصل میشود. این نوع پرسها نسبت به دستگاههای پرس هیدرولیک سریعتر هستند و برای پروژههای سبکتر به کار گرفته میشود.
نکته جالب توجهی که در مورد دستگاه پرس مکانیکی وجود دارد این است که اعمال نیرو از نظر سرعت و بزرگی متغیر است. به همین دلیل هنگام عملیات تولید فشار با استفاده از پرس مکانیکی، باید دامنه صحیح نیروی این دستگاه کنترل شود. این دستگاهها بر اساس مشخصات فرآیند تولید انتخاب میشوند. معمولاً دستگاه پرس مکانیکی در ساخت قطعات فلزی و کار با ورقهها استفاده میشود و نیروی آنها نسبت به پمپهای هیدرولیک پایینتر است. بررسیها نشان میدهد که قدرتمندترین دستگاههای پرس مکانیکی در صنعت تولید مدرن حدود ۱۲ هزار تن نیرو ایجاد میکنند.
دستگاه پرس کرانک یا دستگاه پرس میل لنگی
دستگاه پرس کرانک (Crank Press) از متصل شدن یک میل لنگ به شفت کنترل کننده استفاده میکند. اتصال بین میل لنگ با شفت دستگاه باعث حرکت عمودی چند بالا پایین است. در حقیقت میله اتصالی و میل لنگ باعث تبدیل نیروی چرخشی الکتروموتور به نیروی فشاری میشوند که ممکن است به یک یا چند پیستون به صورت همزمان اعمال شود. بنابراین اگر ما قصد استفاده از دستگاه برای متراکم کردن چند گزینه داشته باشیم، میتوانیم از این گزینه استفاده کنیم.
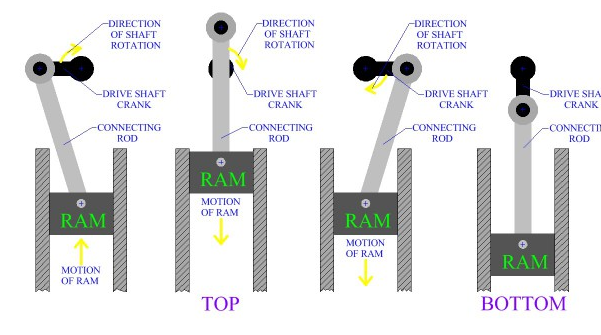
دستگاه پرس کانکل یا اتصال گرهای
دستگاه پرس کانکل (Knuckle Joint Press) انرژی یک الکتروموتور را از طریق یک طراحی اتصالی قدرتمند انتقال میدهد. این دستگاهها عملکردی مشابه با دستگاههای میل لنگ دارند، با این تفاوت که نیرویی اعمال شده و تبدیل این نیرو با استفاده از یک گره در قسمت اتصالی انتقال داده میشود. از این دستگاهها برای کار به صورت عمودی و افقی استفاده میشود و میل لنگ محور به طور کامل میچرخد. به همین دلیل کار با آنها در فشارهای مختلف بسیار راحتتر است و نیروی عظیمی به قطعه کار وارد میکند.
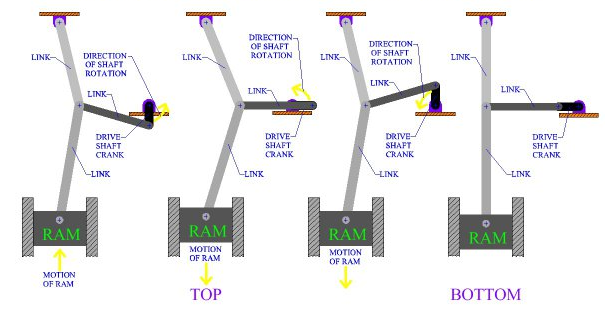
دستگاه پرس گریز از مرکز
در دستگاه پرس گریز از مرکز (Eccentric Press) از یک الکتروموتور برای کنترل یک صفت خارج از مرکز استفاده میشود که در یک میله اتصالی میچرخد. میله اتصالی این دستگاهها در داخل یک مفصل کشویی قرار دارد که حرکت آن در داخل این مفصل باعث بالا رفتن و پایین آوردن پیستون دستگاه میشود. این میله در مرکز قرار نمیگیرد و به همین دلیل با عنوان دستگاههای گریز از مرکز و خارج از مرکز شناخته میشوند. حرکت الکتروموتور به شکلی است که موقعیت شفت در گذر زمان تغییر میکند و این حرکت باعث بالا رفتن و پایین آمدن پیستون و در نتیجه وارد آوردن فشار برای پرس کردن قطعه کار میشود.
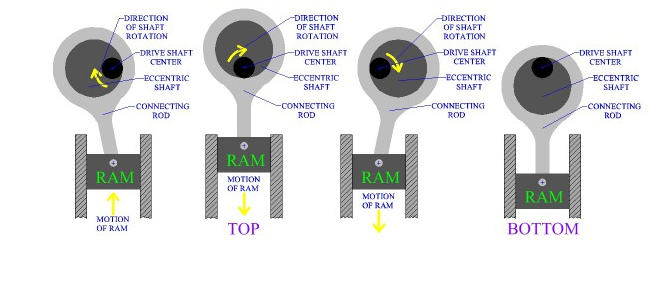
دستگاه پرس دندهای
دستگاه پرس دندهای (Rack And Pinion Press) انرژی تولید شده در الکتروموتور را با استفاده از یک چرخ دنده مستقیماً به یک سمت انتقال میدهد و این فشار به عنوان فشار متراکم کننده استفاده میشود. در حقیقت نیروی تولید شده در الکتروموتور منجر به چرخش یک چرخ دنده در اندازههای مختلف میشود که این چرخ دندهها بر روی یک محور به صورت دندانه دار حرکت میکند. نکته جالب توجه در مورد این دستگاهها این است که حرکت آنها یک بعدی بوده و امکان تنظیم سرعت و تنظیم مقدار فشار در آنها وجود دارد.
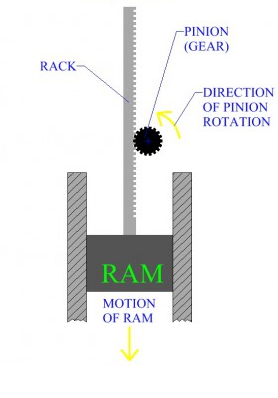
دستگاه پرس پیچ دار
دستگاههای پرس پیچ دار (Screw Presses) از چرخش یک موتور برای چرخاندن یک پیچ بزرگ استفاده میکند. نمونه اولیه دستگاههای پرس به این شیوه طراحی شده بودند و اپراتور میتوانست با چرخاندن یک دسته، به مانند سفت کردن یک پیچ، فشار دلخواه خود را بر روی سطح قطعه کار وارد کند. اما در دستگاههای جدید از یک الکتروموتور برای چرخاندن این پیچ و سفت کردن آن استفاده میشود. این دستگاهها مانند دستگاه های پرس هیدرولیک بسیار کند هستند و نیاز به زمان بیشتری دارند. البته نباید فراموش کرد که برای فشار ثابت نیرو انتخاب فوق العاده ای هستند و دستگاههای جدید آنها ۳۱ هزار تن نیرو بر روی قطعه کار اعمال میکنند.
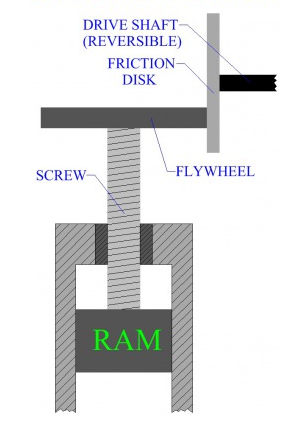
در اینجا تلاش کردیم که ضمن معرفی نحوه عملکرد دستگاه پرس، مدلهای مختلف آنها را هم در بازار معرفی کنیم که طبیعتاً ممکن است هم از لحاظ اندازه و هم از لحاظ کیفیت ساخت با یکدیگر متفاوت باشند. در مطالب بعدی تلاش خواهیم کرد که هر کدام از این دستگاههای پرس را به صورت جزئیتر و کاملتر معرفی کنیم.
گپ ها و NP های بریده شده در مرحله قبل برای استفاده در مرحله مونتاژ توسط دستگاه لبه و پرس دارای انحنا و لبه های موردنیاز می شوند
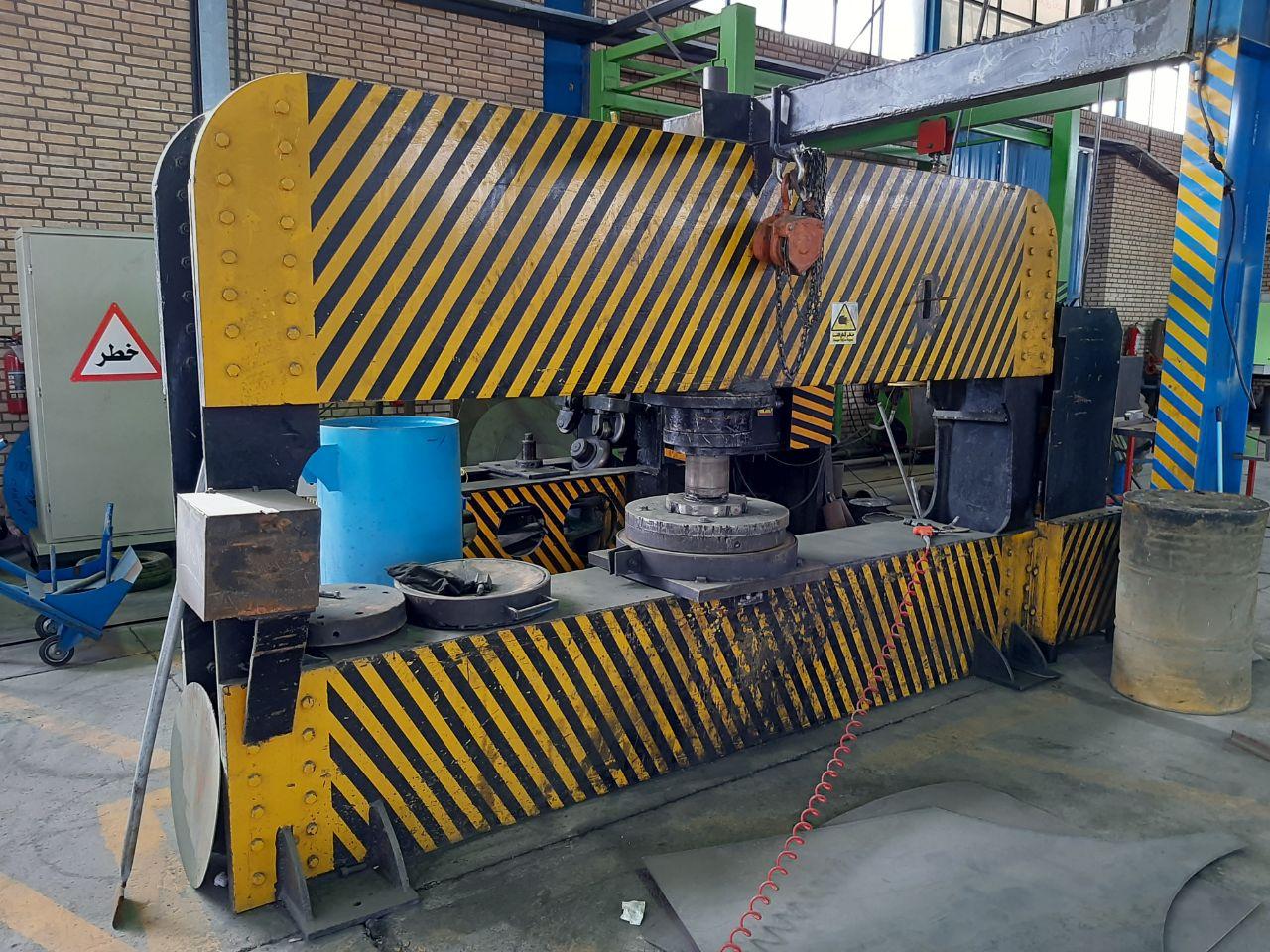
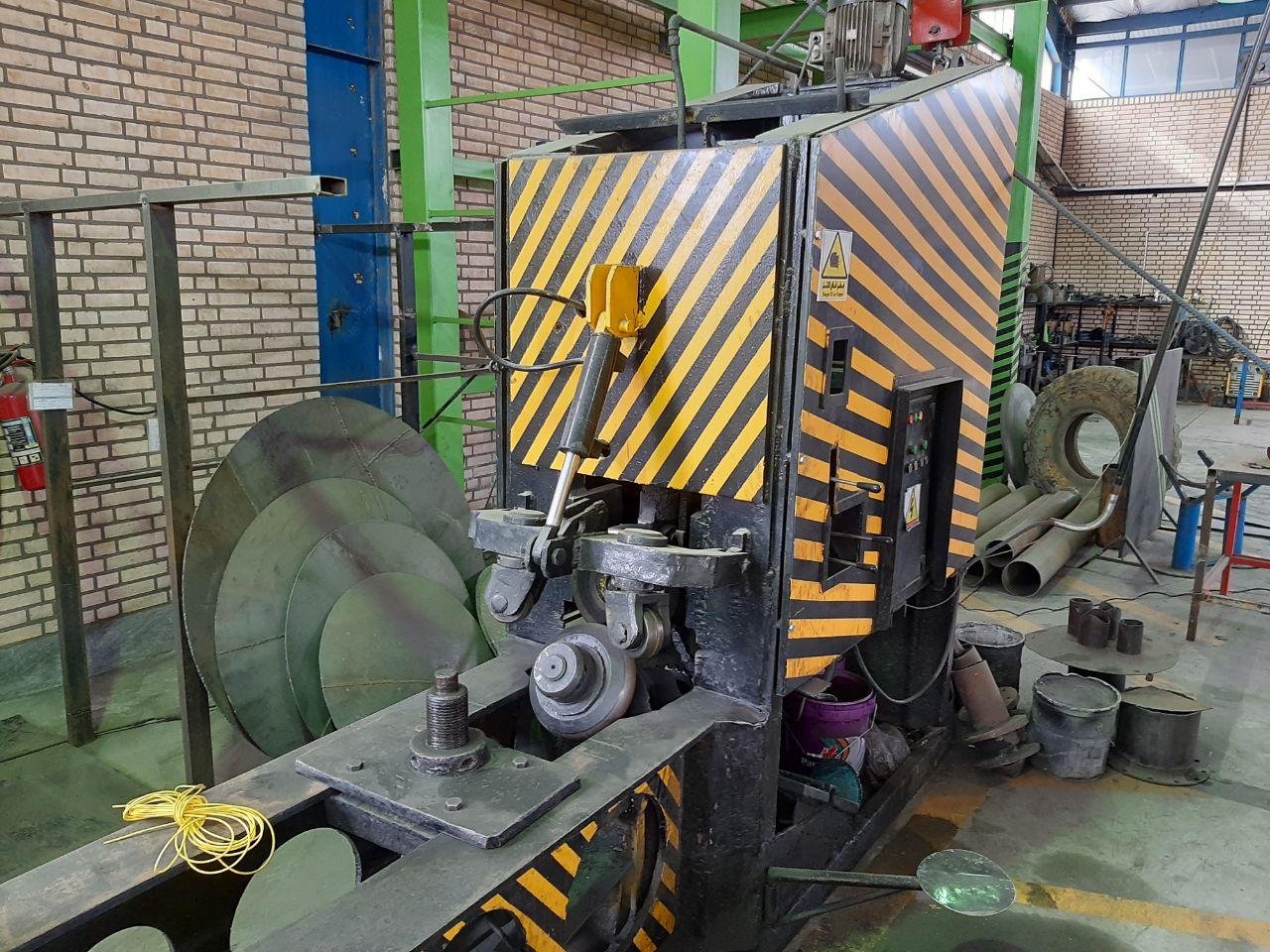
5 ) واحد جوش
جوشکاری چیست ؟ جوشکاری یکی از بهترین و قدیمی ترین روش های مورد استفاده در صنعت به منظور اتصال دو قطعه می باشد، این فرآیند متناسب با نوع مواد مورد استفاده و یا محل انجام آن راهکار های مختلفی را پیش روی مهندسان و تکنسین هایی که به نوعی با جوشکاری سرو کار دارند قرار می دهد .
جوشکاری را میتوان فرآیندی دانست که در آن دو قطعه ی فلزی و حتی غیر فلزی بوسیله ی گرم کردن محل اتصال و یا ذوب کردن مواد اتصال به یکدیگر متصل می شوند .
گرم و ذوب کردن مواد از روش های مختلفی قابل انجام است از این رو جوشکاری نیز دارای انواع و روش های مختلفی می باشد که از جمله روش های اصلی آن ها می توان به موارد زیر اشاره کرد :
- جوشکاری در حالت جامد
- جوشکاری مقاومتی
- جوشکاری با گاز اکسیژن
- انواع متفرقه ی جوشکاری
- سایر روش های متفرقه …
انواع روش های جوشکاری چیستبوسیله قوس الکتریکی
جوش کاری تنگستن گاز ( جوشکاری تیگ – TIG )
در این نوع از جوشکاری الکترود ها مصرف نمی شوند و فرآیند اتصال در آن به صورت آهسته انجام می شود ، در این روش می توان دقیق ترین جوشکاری ها را انجام داد که بیشترین کاربرد آن در صنایع هوا و فضا می باشد .
جوشکاری بوسیله قوس پلاسما
این نوع جوشکاری چیست بیشترین شباهت را به جوشکاری تنگستن دارد و کاری بسیار با کیفیت تولید می کند، عمده مصرف این نوع جوشکاری در صنایع ابزار سازی و یا لوله سازی می باشد .
جوشکاری به همراه پوشش فلزات
در این نوع از جوشکاری الکترود ها مصرف شده اما وجود پودر در این فرآیند از تماس فرآیند جوشکاری با هوا جلوگیری می کند .
جوشکاری فلزی بدون پوشش
در این نوع از جوشکاری دقیقا بر عکس حالت قبلی عمل شده و الکترود ها به صورت کامل مصرف می شوند .
جوش زیرپودری
در این روش از پودر های دانه ریز به منظور پوشش محل اتصال استفاده می شود .
جوشکاری اتمی هیدروژن
در این نوع از جوشکاری از دو الکترود غیر همسان فلزی استفاده می شوند ، این الکترود ها در فضایی مملو از هیدروژن ذوب شده و قطعات را به هم متصل می کنند .
جوشکاری با قوس الکتریکی به همراه پوشش گاز ( TIG )
در این نوع از جوشکاری از گاز به منظور پوشش قطعات استفاده می شود ، از متداول ترین روش های جوشکاری تیگ می توان به جوش آرگون اشاره کرد .
انواع جوشکاری با گاز اکسیژن
جوشکاری با گاز پروپان
در این نوع از جوشکاری که در صنعت به جوش اکسیژن معروف است، پروپان به همراه گاز اکسیژن سوخته و محل اتصال را گرم می کنند .
جوشکاری بوسیله گاز و فشار
در این نوع از جوشکاری ابتدا از شعله برای گرم کردن و سپش از فشار برای اتصال استفاده می شود این نوع از جوشکاری در حال حاضر منسوخ شده و استفاده نمی شود .
جوشکاری هوا استیلن
در این نوع از جوشکاری از مواد شیمیایی به منظور بهبود دهنده فرآیند جوشکاری استفاده می شود ، این نوع از جوشکاری دارای نقاط ضعف بسیار بالایی هستند که به همین دلیل از طرفداران بسیار کمی برخوردار هستند .
جوشکاری با اکسیژن استیلن
در این نوع از فرآیند های جوشکاری بوسیله ترکیب اکسیژن و استیلن قطعات را تا دمای بسیار بالا گرم می کنند و این دمای زیاد باعث بوجود آمدن جوش بسیار دقیق می شود ، از دیگر مزیت های این نوع جوشکاری ارزان بودن موارد مورد استفاده در آن می باشد .
جوشکاری اکسیژن هیدروژن
در این نوع از جوشکاری از ترکیب هیدروژن و اکسیژن به منظور ایجاد جوش استفاده می شود .
انواع جوشکاری چیست و جوشکاری مقاومتی
جوش درز مقاومتی
این نوع جوشکاری یکی از در دسترس ترین و متداول ترین روش های جوشکاری و روش های اصل قطعات است،در این مدل از جوشکاری عملیات جوش و اتصال دو الکترود رول شکل که با اعمال جریان و فشار گرم می شوند انجام می شود .
جوش آپست
در جوشکاری آپست که به منظور اتصال لبه های قطعات مورد استفاده قرار می گیرد تا دمایی مشخص و متناسب با جنس کار گرم شده و با فشار بسیار بالا به هم متصل می شوند، این نوع از گرمایش به وسیله مقاومت و جریان الکتریکی ایجاد می شود .
جوش نقطهای مقاومتی
این نوع از جوشکاری در صنعت خودرو سازی و هوا فضا مورد استفاده قرار می گیرد و از دو الکترود نوک تیز به منظور اتصال دو نقطه که عموما ضخامت کمی دارند مورد استفاده قرار می گیرند .
در شرکت آبین گستر شرق گرمسار از جوش های زیرپودری ، CO2 و دستی برای جوش قسمت های مختلف دستگاه ها استفاده میشود .
شرکت آبین گستر به منظور افزایش کیفیت جوش مورد استفاده در محصولات خود تمامی پرسنل واحد جوش را با همکاری سازمان فنی و حرفه ای کشور آموزش داده و گواهینامه های لازم در این بخش را دریافت کرده است
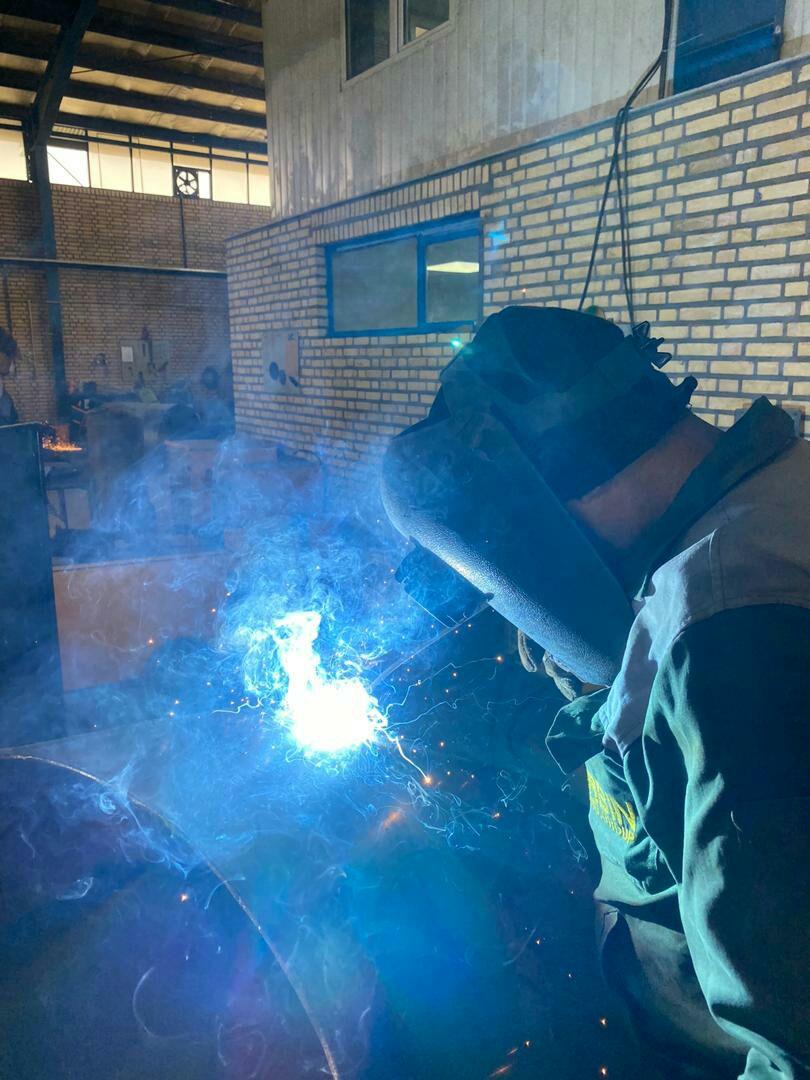
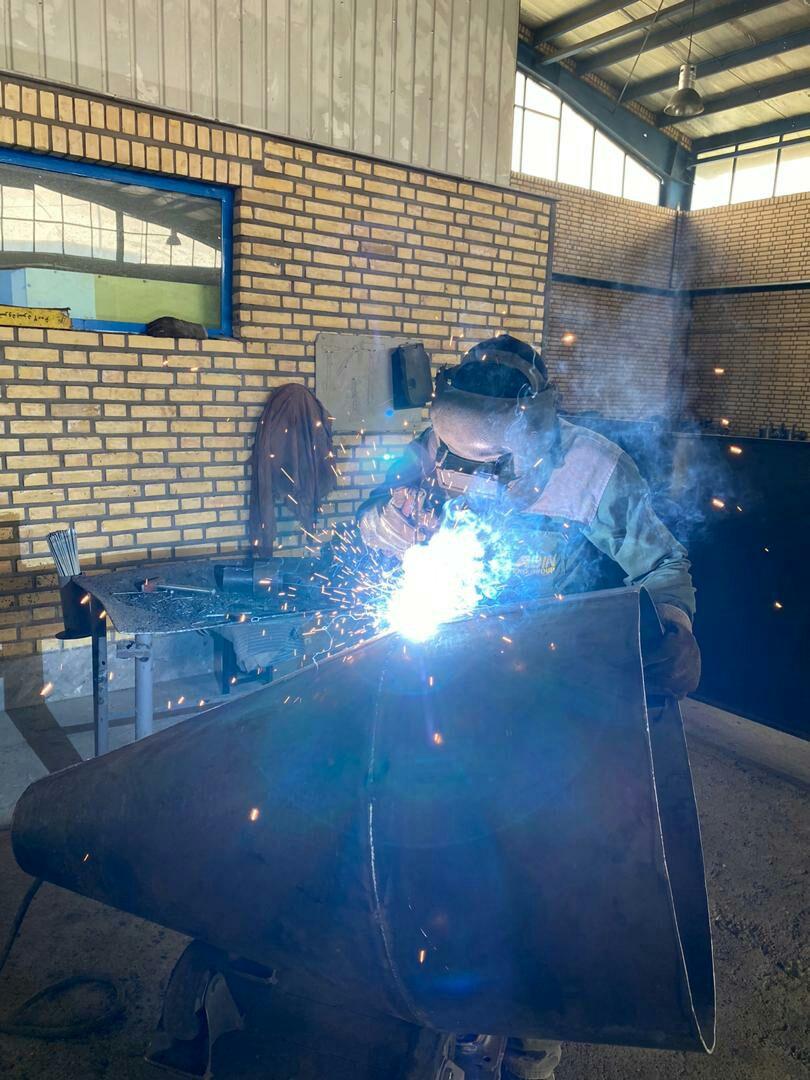
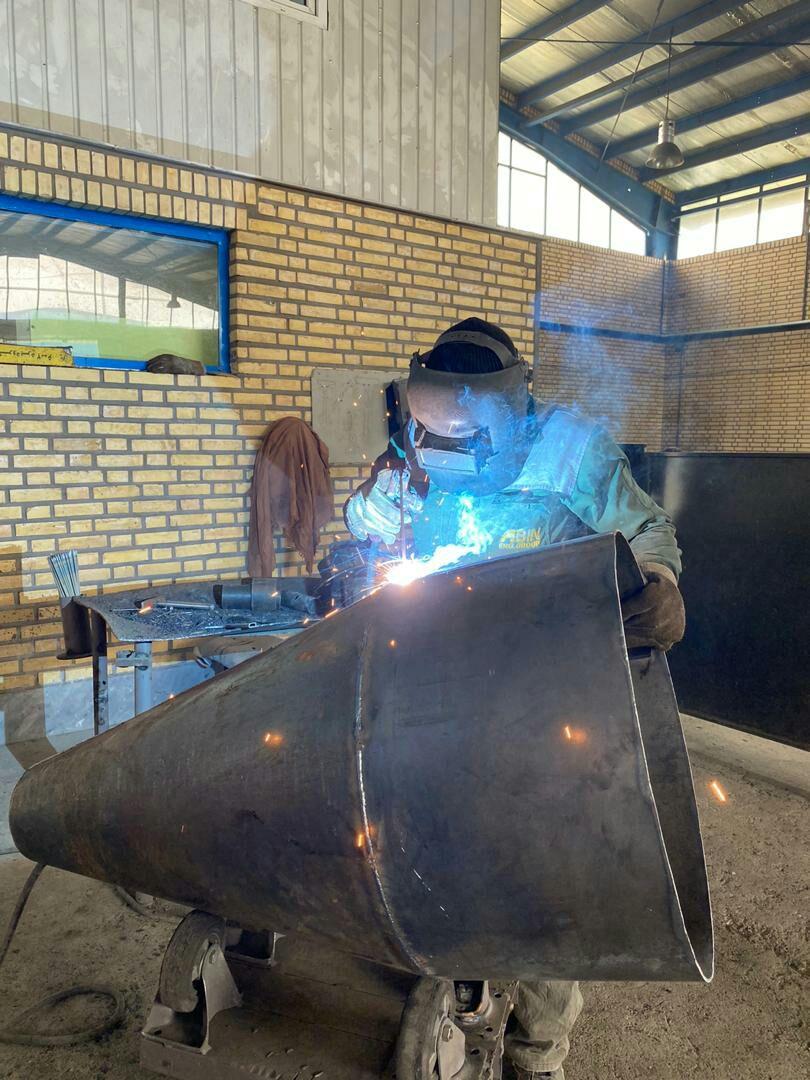
6 ) واحد مونتاژ
مونتاژ (به فرانسوی: Montage) یک وام واژه از زبان فرانسوی است که به فارسی وارد شده است و در معنیهای زیر بکار میرود:
- خط مونتاژ به معنی سرهم کردن یا وصل کردن قطعات صنعتی پیشساخته مانند قطعات خودرو
دستگاه های تولید شده در بخش های مختلف قبل از رنگ کاری مونتاژ شده و سپس وارد واحد رنگ میشوند
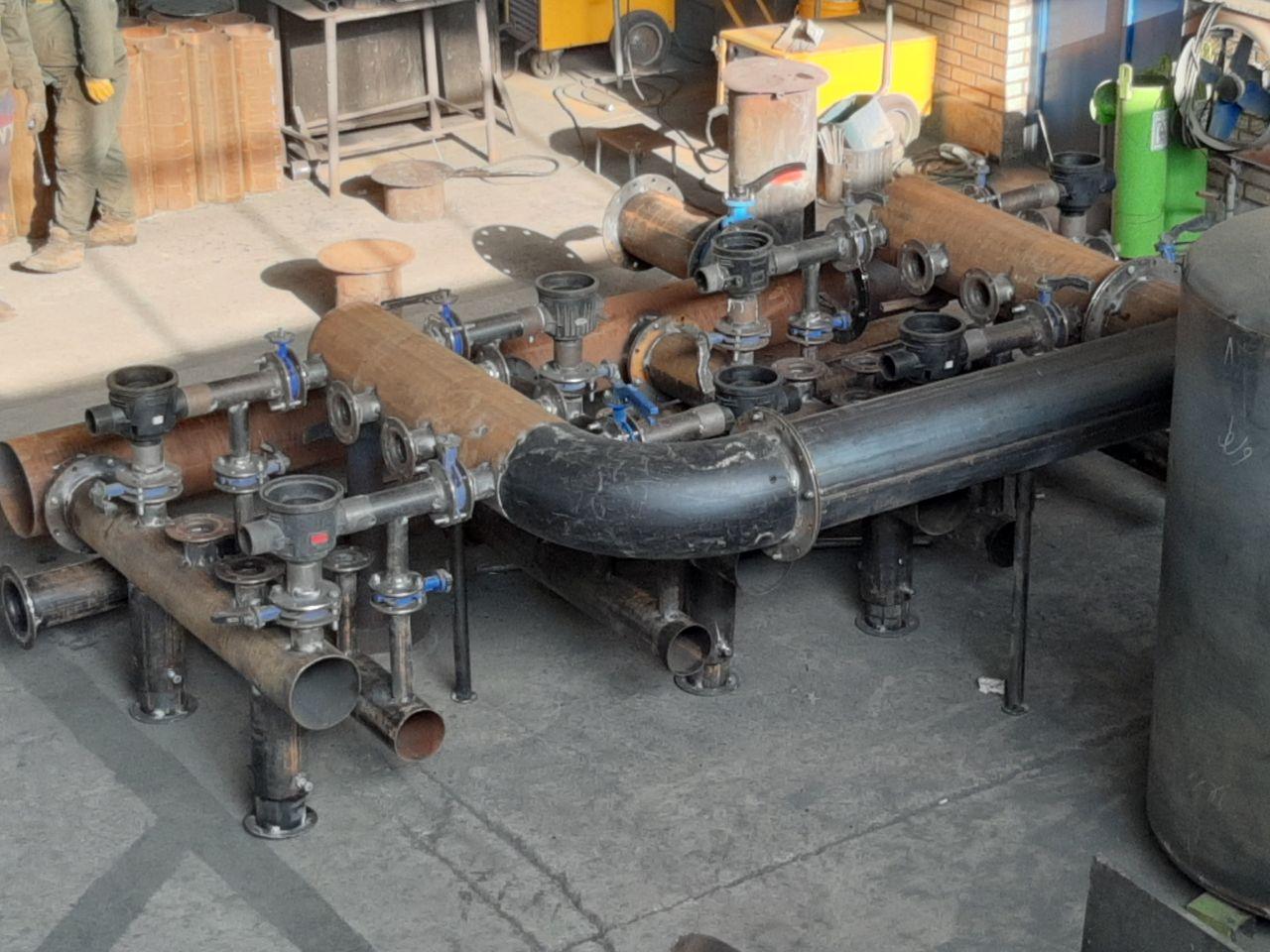
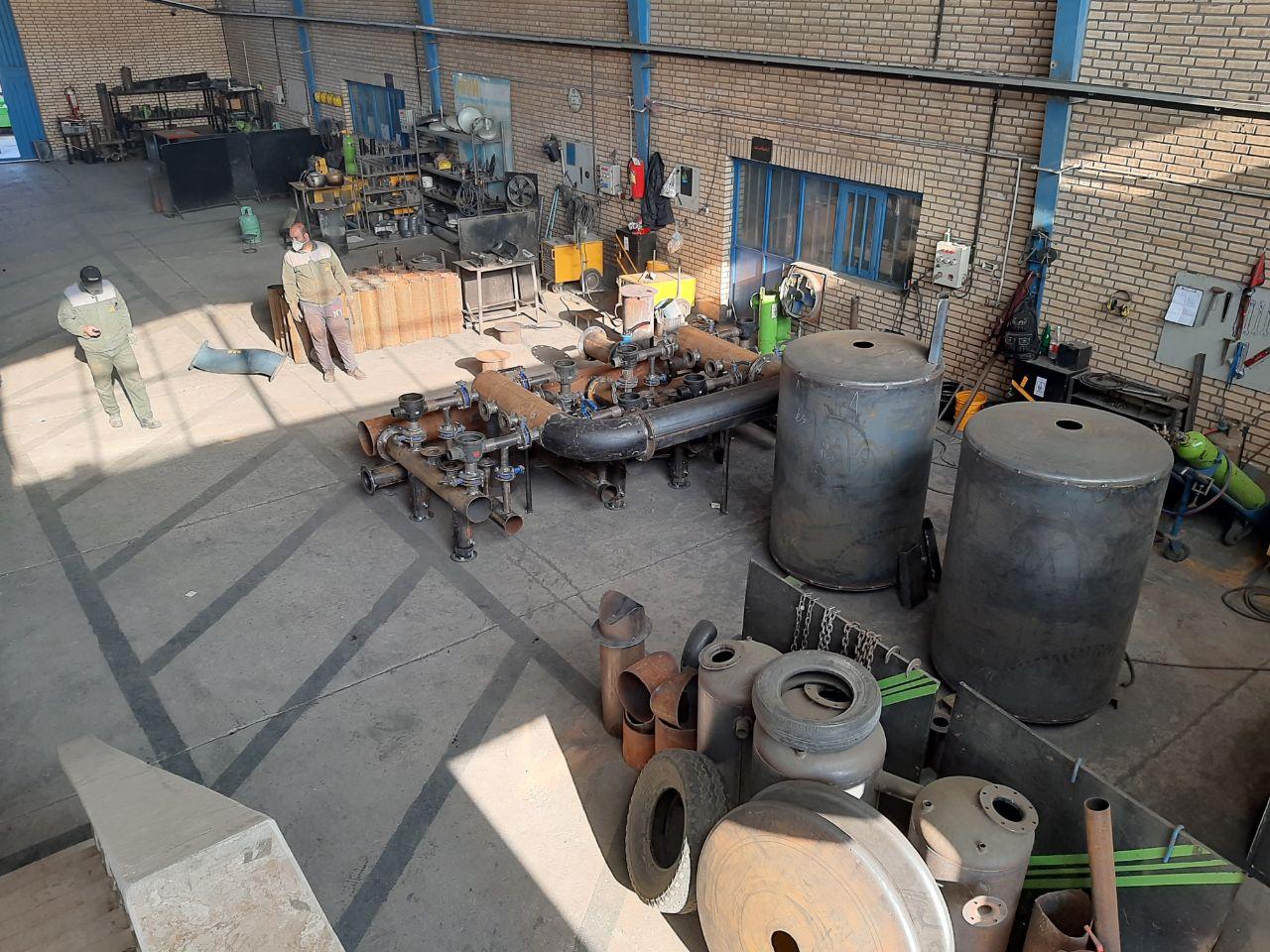
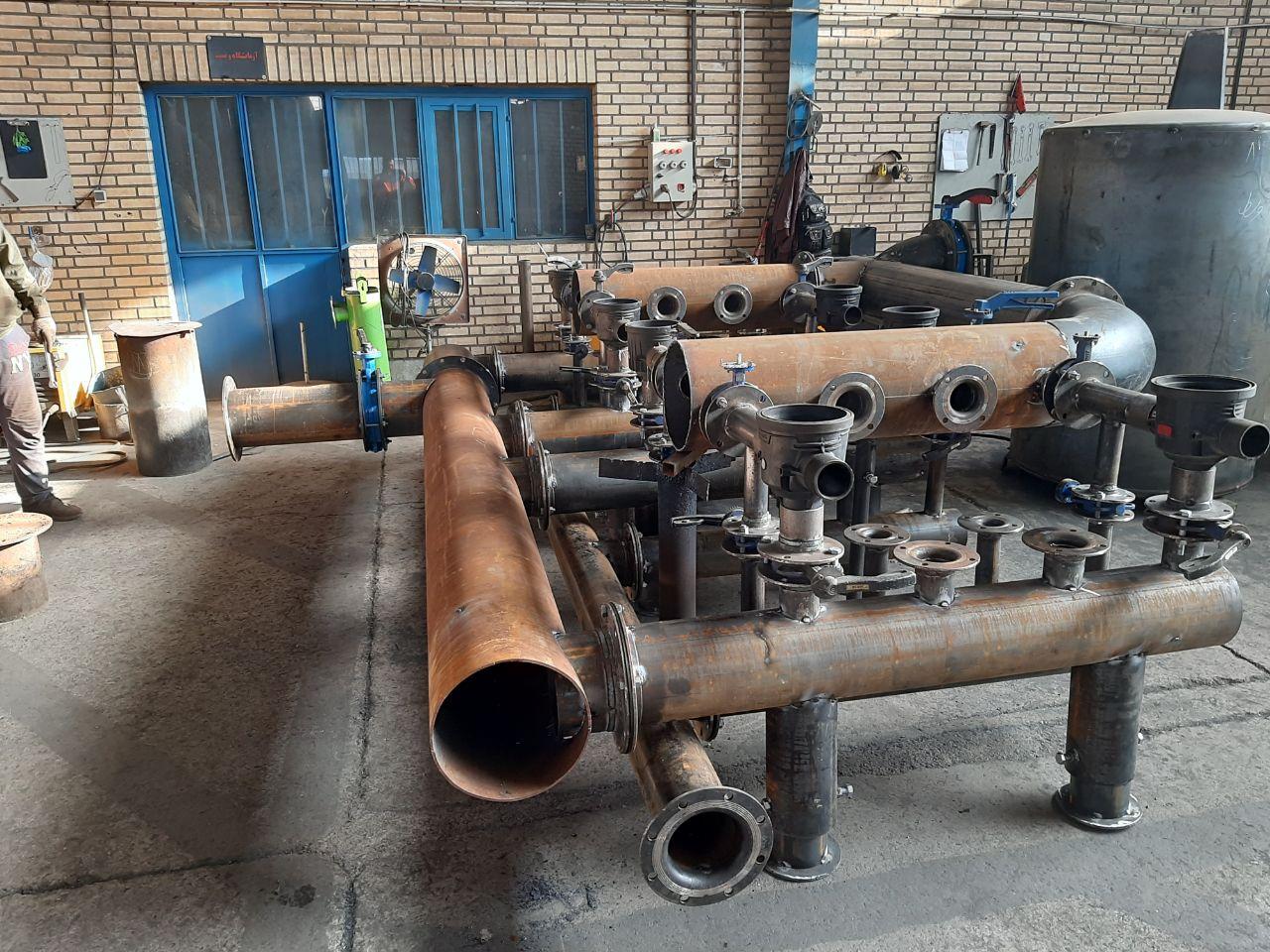
7 ) واحد تمیزکاری
دستگاه های ساخته شده در مراحل قبل توسط واحد تمیزکاری طی عملیات فرچه زنی ، سنگ زدن آماده تحویل به واحد رنگ میشوند
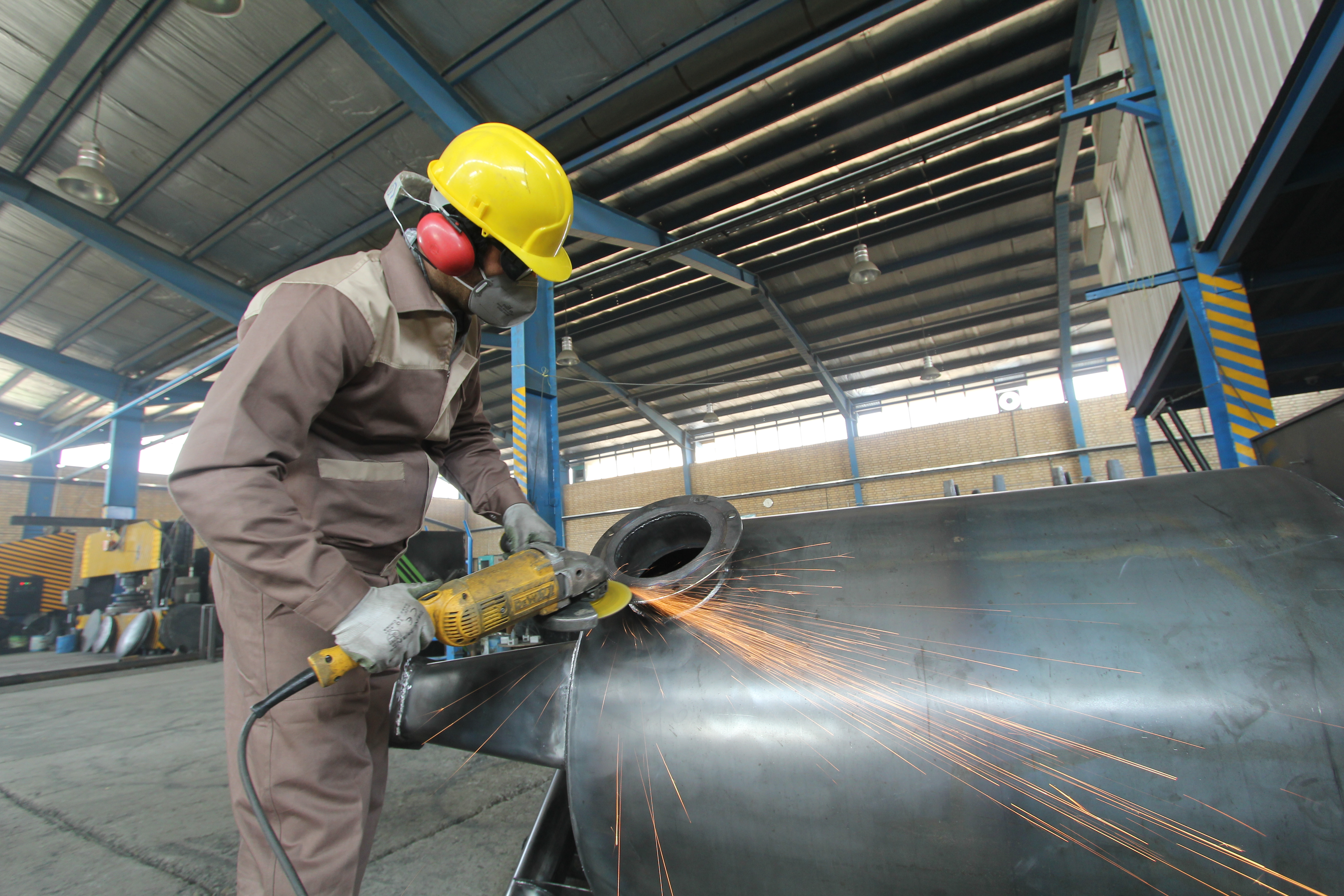

8 ) واحد رنگ
دستگاه های تولید شده در مراحل قبل در این قسمت از داخل یک لایه رنگ بنام کولتاراپوکسی و از بیرون یک لایه بنام اپوکسی پرایمر بعنوان آستر و یک لایه پلی اورتان بعنوان رنگ نهایی شده و به مدت 24 ساعت در فضای مناسب برای خشک شدن قرار خواهند گرفت .
رنگ صنعتی چیست؟
پیش از معرفی رنگ صنعتی اپوکسی باید گفت که رنگ صنعتی به طور کلی صنایع نفت، گاز و پتروشیمی، بزرگترین صنعتی است که در آن رنگ صنعتی مورد استفاده قرار می گیرد. رنگ صنعتی در ایران این طور مرسوم شده است و به رنگ هایی گفته می شود که کاربرد آن تنها در زیباسازی و یا علامت گذاری نباشد. به عنوان مثال رنگ ساختمانی روغنی یا رنگ ساختمانی پلاستیک و همچنین رنگ اکریلیک به عنوان رنگ های دکوراتیک شناخته شده و جهت زیباسازی محیط داخلی و یا خارجی ساختمان مورد استفاده قرار می گیرد. همچنین رنگ ترافیکی نیز با توجه به صنعت کاملا مجزا و کاربری آن، که تنها برای علامت گذاری جاده ها و ابزارهای ترافیکی مورد استفاده قرار می گیرد، در دسته بندی جداگانه ای قرار می گیرد.
مهم ترین خصوصیتی که از رنگ صنعتی آن انتظار می رود، خاصیت ضد خوردگی آن است. در درجه اول رنگ صنعتی به این منظور مورد استفاده قرار می گیرد که از سطح فلز یا هر زیرآیند دیگری محافظت شده و از خوردگی و زنگ زدگی آن جلوگیری به عمل آید.
انواع رنگ های صنعتی
جهت دسته بندی رنگ صنعتی می توان شرایط مختلفی را در نظر گرفت. به عنوان مثال می توان براساس نوع رزین، نوع حلال و یا لایه مصرفی رنگ، دسته بندی هایی را انجام داد. رنگ صنعتی اپوکسی، رنگ صنعتی پلی یورتان، رنگ صنعتی کولتار اپوکسی و… در دسته بندی رزین قرار گرفته و رنگ صنعتی پایه حلالی، رنگ صنعتی پایه آب، رنگ صنعتی بدون حلال یا solvent free در دسته بندی حلالی قرار داده می شود. همچنین رنگ صنعتی آستر، رنگ صنعتی میانی، رنگ صنعتی رویه نیز بر اساس لایه مصرفی دسته بندی شده است. مهم ترین و پرکاربرد ترین دسته بندی، دسته بندی براساس نوع رزین است.
معرفی رنگ صنعتی اپوکسی
برای معرفی رنگ صنعتی اپوکسی باید به این نکته اشاره کرد که این رنگ در تمامی صنایع نفت و گاز و پتروشیمی، صنایع آب و فاضلاب، صنایع فولاد، صنایع استراکچرسازی، صنایع نیروگاهی و سایر صنایعی که در آن حفاظت از فلز و جلوگیری از خوردگی مهم می باشد، کاربرد بسیار وسیعی داشته و در حقیقت مهم ترین نوع رنگ صنعتی به شمار می آید.
این رنگ مقاومت بسیار مناسبی در برابر عوامل خوردگی داشته و بیشتر به عنوان لایه آستری و لایه میانی مورد استفاده قرار می گیرد. ضعف این رنگ، عدم مقاومت در برابر اشعه UV خورشید می باشد که باعث می گردد نتوان در محیط باز به عنوان لایه نهایی مورد استفاده قرار داد. انواع رنگ صنعتی اپوکسی را به شرح ذیل می توان معرفی نمود:
رنگ صنعتی آستر زینک ریچ اپوکسی zinc rich epoxy primer
رنگ صنعتی آستر زینک کرومات اپوکسی zinc chromate epoxy primer
رنگ صنعتی آستر زینک فسفات اپوکسی zinc phosphate epoxy primer
رنگ صنعتی آستر اکسید آهن اخرایی اپوکسی iron oxide epoxy primer
رنگ صنعتی میانی High build اپوکسی پلی آمید High build epoxy mid coat
رنگ صنعتی میانی MIO اپوکسی پلی آمید Mio epoxy mid coat
رنگ صنعتی رویه اپوکسی پلی آمید epoxy top coat
رنگ صنعتی آستر اپوکسی پلی آمین مقاوم شیمیایی epoxy polyamine primer
رنگ صنعتی رویه اپوکسی پلی آمین مقاوم شیمیایی epoxy polyamine mid coat
رنگ صنعتی اپوکسی پلی آمین گلس فلیک Glass flake epoxy polyamine
9 ) واحد بسته بندی و بارگیری
در این واحد آخرین اقدامات جهت بسته بندی و ارسال صورت میگیرد
10 ) واحد کنترل کیفیت
اهداف:
این واحد با بهره بردن از کارشناسان دارای صلاحیت، روش هایی را تدوین می نمایند تا کارخانه بتواند به وسیله ی آن روش ها، از مرغوبیت و مشتری پسند بودن کالاهای تولیدی خود مطمئن گردد. که از مهمترین اهداف این واحد:
تشکیل جلسات منظم و حضوری برای افزایش بازده کیفی کارخانه
بازرسی و کنترل کیفیت مواد اولیه، فرآیند تولید و محصول نهایی به منظور ارتقای کیفیت محصولات
انجام تست ها بر اساس استانداردهای ملی و بین المللی بر روی مواد اولیه در آزمایشگاه مواد به منظور اطمینان از کیفیت مدنظر
تولید محصولاتی با کیفیت در سطح جهانی در جهت جلب رضایت مشتریان
در تمام مراحل فرآیند تولید واحد کنترل کیفیت بازرسی و نظارت مواد و قطعات اولیه ، برش ، نورد ، پرس و لبه ، جوش ، مونتاژ و رنگ و بسته بندی و بارگیری و ارسال دستگاه های تولید شده را بر عهده دارد .
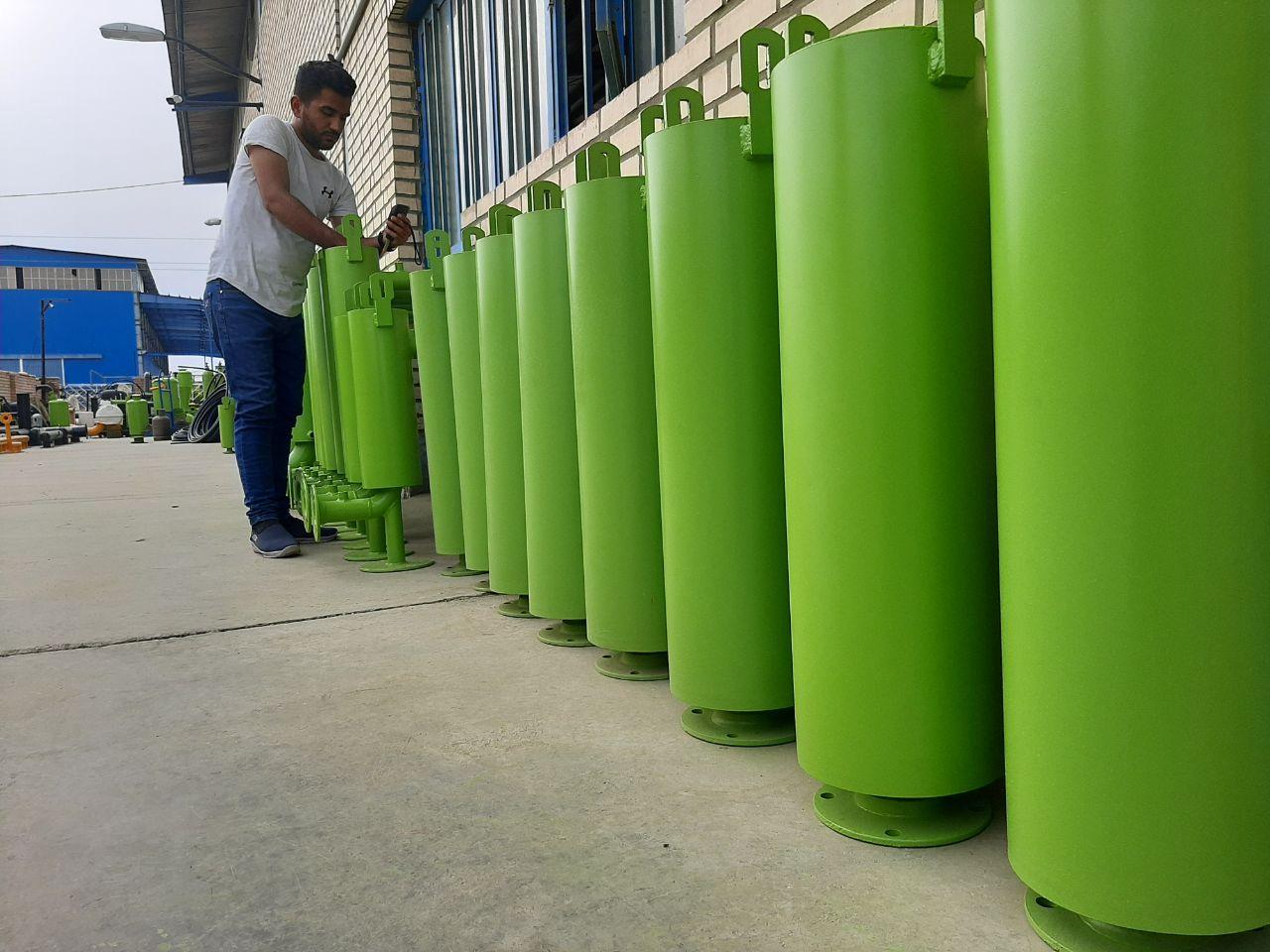
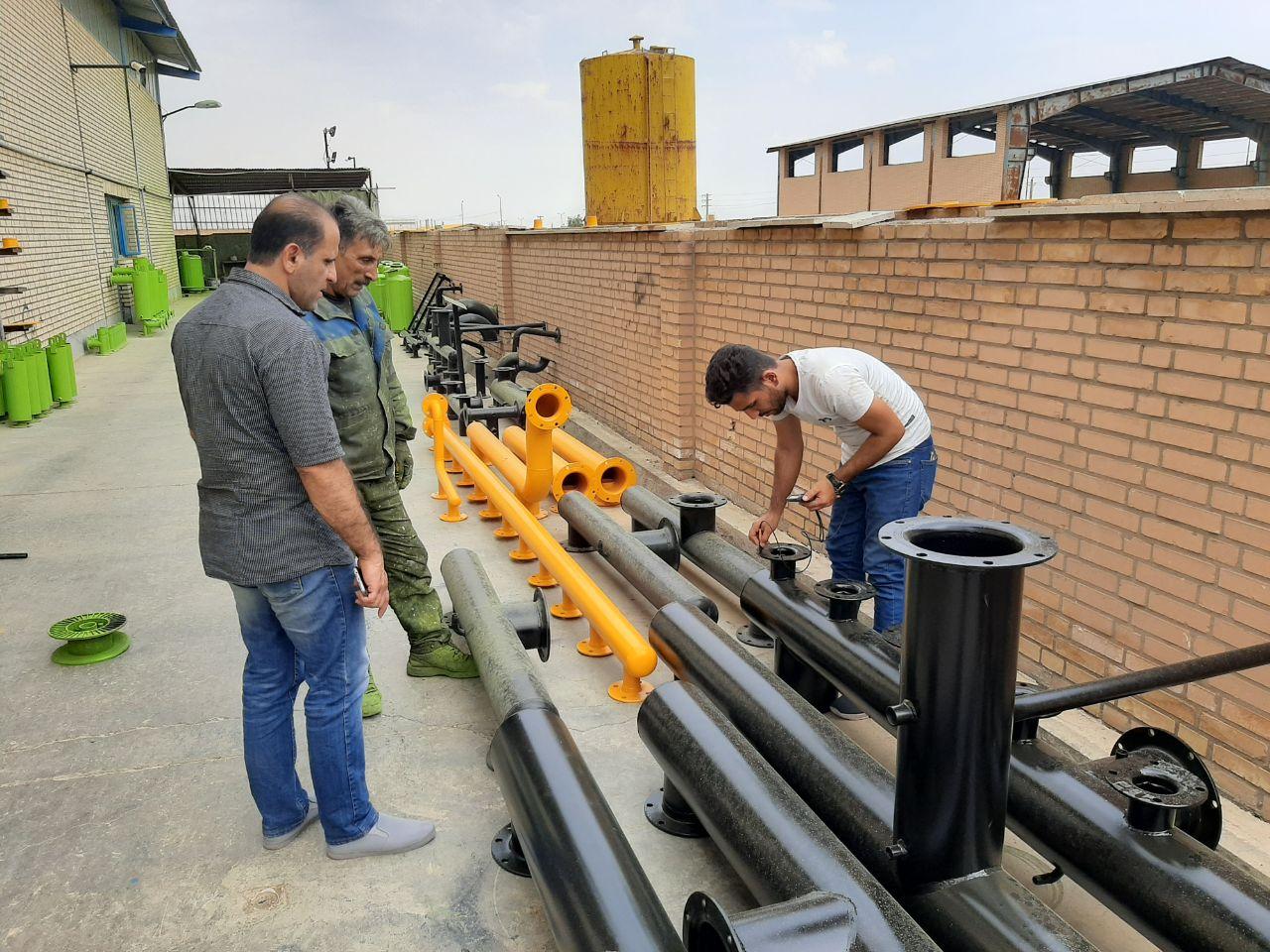
۱۳۹۹/۲/۲۹
بازدید:
932